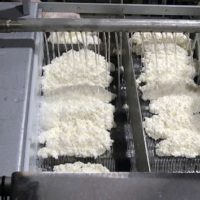
(SUWON, South Korea) — South Korean conglomerate CJ Cheiljedang is jumping into the global market to begin mass production of PHA biodegradable plastic, or polyhydroxyalkanoates.
PHA is considered a viable alternative to petroleum-based plastic because the new technology allows its plastic waste to decompose completely in the ocean and soil in a significantly shorter period of time.
“Plastics made from crude oil are said to take over 500 years to completely decompose, while biodegradable plastics take decades at most,” SungYeon Hwang, Head of Bio-based Chemistry Research Center at the Korea Research Institute of Chemical Technology, told ABC News. “Biodegradable plastic does not pollute the sea even if it accidentally flows into the shore.”
This next generation of plastic, PHA — made from microorganism fermentation — is currently manufactured by U.S. company Danimer, based in Bainbridge Georgia, and Japanese company, Kaneka.
CJ Cheiljedang aims to construct a 5,000 tons worth PHA manufacturing line in Indonesia by the end of this year. The global bioplastic production market is anticipated to reach up to 2.8 million tons by 2025, according to the European Bioplastics’ market analysis in 2020.
The inevitable move from petroleum-based plastic to an eco-friendly substitute has been exacerbated by Europe’s sales ban of the 10 most commonly found plastic waste items at the bottom of the ocean such as straws, takeout containers and water bottles made of polystyrene.
“With PHA, CJ Cheiljedang hopes to play a leading role in changing the paradigm of the global materials market,” CJ Cheiljedang’s communications team told ABC News. “’Going green’ is an inevitable trend in all industries.”
CJ Cheiljedang’s PHA has been certified biodegradable in industry use, household compost, soil and water by TUV Austria, an institution for biodegradability testing and certification.
From microorganism to eco-friendly plastic
Making solid PHA material begins by engineering and creating microorganisms. At CJ Cheiljedang lab in Suwon, just south of Seoul, researchers grow and nurture microorganisms and select the strongest strain through automated machines.
“These selected strains are optimally grown in a controlled environment where we tightly regulate the shaking speed and temperature,” Researcher Park Yae-seul told ABC news.
The chosen strains go through a fermentation process during which the cells are grown in bioreactors and subsequently fed with sugar made from feedstock for better production of PHA.
After a certain period of fermentation, the materials go through a refinery process where PHA are dehydrated and aggregated before being made into long strands of liquid plastic, which later dries up into solid biodegradable plastic materials.
Shortfalls of PHA
While a number of biodegradable materials have been proposed as a solution to the global plastic pollution problem, there is still much controversy over how the biodegradable plastic waste is disposed of.
“Ideally, it is best to collect used PHA-based plastic waste and process them in an industrial compost in order to meet its biodegradable characteristics,” In-Joo Chin, president of the Korean Bioplastics Association, told ABC News.
Bioplastics like PHA are, theoretically, compostable if collected and buried separately but, for now, consumers are advised to throw them away together along with general waste.
The amount of commercial waste at this point is not enough to design a separate collecting system, experts say. PHA will only become an effective eco-friendly alternative for plastic when its manufacturing reaches an adequately sized economy of scale in the future.
CJ Cheiljedang, as a starter to its next generation makeover, has recently begun wrapping their tofu bundle with vinyl packaging containing their own PHA as a test use in consumer goods. But reaching economies of scale is still a long way off.
“The cost of replacing the original vinyl packaging made out of petroleum based plastic PP with a biodegradable alternative was more expensive, but we consider the biodegradable plastic market as an economy of scale,” Technology Strategy professional Young Min Lee told ABC News. “As more and more plastics are replaced with biodegradable plastic, the production cost will naturally go down.”
“It will make a big step for a better environment if the plastic waste that has no choice but to go to general waste-straws, such as agricultural munching films, and small containers-are replaced with biodegradable plastic like the PHA,” Hong Soo-yeol, chief researcher at Seoul-based Resource Recycle Consulting, told ABC News.
ABC News’ Hyun Soo Kim contributed to this report.
Copyright © 2021, ABC Audio. All rights reserved.