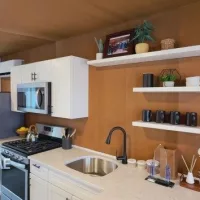
(NEW YORK) — The sawmills of Maine generate a lot of wood waste each year: 1 million tons to be exact. For years, it was just discarded as a byproduct of the lumber industry. Now researchers at the University of Maine’s Advanced Structures & Composite Center (ASCC) have figured out a way of using those wood residuals to create homes.
However, they’re not building them in the conventional way. They’re printing them using the world’s largest 3D printer of its kind.
“We thought, ‘How do we turn that wood waste into something very valuable?'” Habib Dagher, the ASCC’s executive director, told ABC News.
The result is a prototype, 600-square foot home that they’re calling BioHome3D.
The homes are constructed using just two ingredients: wood waste and corn resin. By combing the two ingredients, the ASCC creates pellets for the 3D printer.
“These pellets are fed right into the printer. They’re heated and they’re extruded through a printer head, and that’s how we produce this house, layer by layer,” Dagher explained. “Now this material is what’s 100% renewable, because it is really bio based.”
A BioHome takes about a week to create, is made of material that’s stronger than concrete and is completely recyclable, according to Dagher. He said the house can be broken down into the original pellets and then be used to print something else like another house or a boat, which the ASCC is also 3D printing.
“We’ve done it five times over, so we’ve recycled it five times and looked at what happens to the properties,” Dagher said. “The good news is the properties hold up good enough. So, there’s so many applications for those materials.”
The places where we spend most of our time — buildings — are among the largest producers of greenhouse gas emissions in the world. Building construction and operations are responsible for about 40% of global greenhouse gas emissions and produce about a third of the world’s waste, according to the World Green Building Council. The United Nations Environment Program says the building and construction sector is “by far” the largest emitter of greenhouse gases of any industry in the world.
Dagher said its 3D printing technology reduces the amount of labor needed, the level of waste and allows for all the building materials to be prefabricated in a controlled environment. Sensors placed in and around the home to test how it’s handling the elements show that, over the past three years, it’s performing just like a home manufactured in the traditional way.
Dagher said its 3D printing technology reduces the amount of labor needed, the level of waste and allows for all the building materials to be prefabricated in a controlled environment. Sensors placed in and around the home to test how it’s handling the elements show that, over the past three years, it’s performing just like a home manufactured in the traditional way.
The university is currently building a “factory of the future” to expand its sustainable manufacturing research and production. The new facility will also train a new generation of workers and collaborate with companies on 3D printing projects.
Another company, Miami-based Renco USA, is also building sustainable housing but it’s using interlocking bricks made from recycled materials instead of 3D printers.
“It’s all interlocking, like a Lego, so all the pieces have this same top and bottom component here, and they fit together,” Patrick E. Murphy, managing director of Renco, told ABC News. “They’re as easy as that.”
The bricks are put together using a simple rubber mallet and held in place with adhesive.
The material, molded from repurposed materials like glass fibers and resin — along with stone — is stronger than concrete, fire resistant and designed to withstand a Category 5 hurricane, according to Renco.
Renco just built its first U.S.-based factory, which has the capacity to build 7,000 houses or apartments per year. Its most recent project, a 96-unit complex in Palm Springs, Florida, was built in just eight weeks, the company said.
The process is so simple, it can be adopted by anyone, according to Murphy.
“Anyone who can build a Lego set can build a home using Renco’s blocks,” Murphy said
ABC News’ Climate Unit contributed to this report.
Copyright © 2025, ABC Audio. All rights reserved.